search
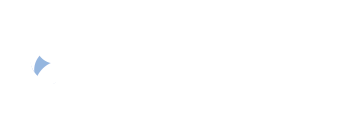

Why Special Alloys?
While 316L / 1.4404 will hold for most applications, some factors such as high chloride media, acidic pH levels, high temperature, time of contact, and equipment design can affect the corrosion of stainless steel. With this in mind, the NEUMO Ehrenberg Group offers a wide range of special alloys. From 316L / 1.4404 and 1.4435 to 904L / 1.4539, AL-6XN® / 1.4529 and Hastelloy C22® / Alloy C22 / 2.4602 as well as Alloy 59 / 2.4605. These alloys are commonly used in the biotech, pharmaceutical, personal care, home care, food, dairy, and beverage industries worldwide. The main concerns of end users, architects and engineers (A&E’s) when choosing a special alloy are microbial contamination, system reengineering, maintenance downturns, production loss and safety of its employees and the environment. Stainless Steel and Corrosion The uniqueness (secret) behind the corrosion resistance of stainless steel is the formation of a durable and spontaneous ultra-thin film that covers the surface. This film consists mainly of chromium oxides and ensures the metallic steel (base metal) is never in contact with the environment. As long as the surface is clean and free of contamination, this film protects the steel in a process known as passivation. The resistance of this film is dependent on the steel grade chosen and the conditions to which it is exposed. If the conditions become aggressive, the oxide film breaks down resulting in corrosion. Finding the proper chemical composition steel will result in a stable oxide film that will be resistant to the relevant type of corrosion. The main types of corrosion affecting hygienic and high purity application in aggressive chloride environments are pitting, crevice, and stress corrosion. Optimum performance is obtained by the use of alloying elements, chromium, molybdenum, and nitrogen, all of which are very effective in improving resistance to pitting and crevice corrosion, and high nickel and nitrogen contents for stress corrosion cracking. When a part of process equipment breaks down, it is vital to determine the cause of the failure to prevent future replacement and production losses. For example, if the piping system is made from 316L and it fails in an aqueous salt environment with high temperature, a special alloy with higher molybdenum could provide a lifelong solution to the system. Types of Alloys and PREN In today’s market there are a wide range of austenitic, superaustenitic, duplex, superduplex, and nickel-base alloys. Besides corrosion performance, other factors should be considered such as commercial availability, appearance, good mechanical properties, and fabrication characteristics. High performance or high corrosion resistance is obtained by using a high level of chromium, nickel, molybdenum and nitrogen and by producing these grades with very low carbon contents to preserve the resistance while allowing hot fabrication and welding. The Pitting Resistance Equivalent Number (PREN), is a predictive measurement of a stainless steels resistance to localized pitting corrosion based on their chemical composition. In general, the higher the PREN-value, the more resistant the alloy is to localized pitting corrosion by aqueous salt solution. ![]() For stainless steel: PREN = %Cr + 3.3 x %Mo + 16 x %N Typical Applications Some of the common applications for the special alloys 904L / 1.4539, AL-6XN® / 1.4529 and Hastelloy C22® / Alloy C22 / 2.4602 in the hygienic, biotech and pharmaceutical industries are as follows.
Product range Superaustenitic – 904L / 1.4539 and AL-6XN® / 1.4529 The superaustenitic also known as high-performance stainless steel share many characteristics with its standard grade counterpart such as high tensile strength, good weldability, and formability becoming a better choice than duplex stainless steel. Additionally, it is a cost-effective alternative to more expensive nickel-base alloys. AL-6XN® / Ultra 6XN / 1.4529 / UNS N08367 Pharmaceutical and Hygienic Tube & Fittings • Standard: ASME-BPE • Sizes: 1/2” - 4” O.D. tube size • Internal Surface Finish: SF1- 0,51μm (20Ra) & SF5 - 0,51μm (20Ra) EP • Tube complies with ASTM A270/A249/B676 and ASME SA249/SB676. MTR according EN 10204-3.1 904L / 1.4539 / UNS N08904 Pharmaceutical and Hygienic Tube & Fittings • Standard: DIN11866 / DIN11865 range B • Sizes: DN8 (13,5) - DN100 (114,3) • Internal Surface Finish: H3 (internal Ra < 0,8µm) & HE3 (internal Ra < 0,8µm EP) • Tube complies with EN10217-7/DIN11866/AD2000-W2. MTR according EN 10204-3.1 Pharmaceutical and Hygienic Tube & Fittings • Standard: ASME-BPE • Sizes: 1/2” - 4” O.D. tube size • Internal Surface Finish: SF3 - 0,76 μm (30Ra) & SF4 - 0,38μm (15Ra) EP • Tube complies with ASTM A269/A249/B674/B677 and ASME SB674/SB677. MTR according EN 10204-3.1 Nickel-based alloy – Hastelloy C22 ® / Alloy C22 / 2.4602 HASTELLOY Alloy C-22® / Alloy C22 is a nickel-chromium-molybdenum alloy with enhanced resistance to corrosion. The alloy provides exceptional resistance to pitting and crevice corrosion attacks in chloride-induced media as well as stress corrosion cracking. Hastelloy® C-22® / Alloy C22 / 2.4602 / UNS N06022) Pharmaceutical and Hygienic Tube & Fittings • Standard: ASME-BPE • Sizes: 1/2” - 4” O.D. tube size • Internal Surface Finish: SF1 - 0,51μm (20Ra) & SF5 - 0,51μm (20Ra) EP • Tube complies with ASTM B626/B622 and ASME SB626/SB622. MTR according EN 10204-3.1 |